

















Development in 2011-2014 supported by:
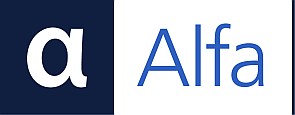
|
Introduction
This experimental campaign was performed in our department at the CTU in Prague
on samples from Aircraft Industries company. These were originally manufactured by Acorn Welding
to serve for component tests of welded joints for the project of a new engine bed for L 410 NG airplane.
The project was abandoned, however. We proposed to test the samples in our lab under the condition
that the test output will be free for any publication. The results should primarily serve as an experimental basis
for diploma and PhD theses in our department, but thanks to their open-access character their wide sharing
in other projects is enabled.
Jan Papuga
Conditions of Use
In case you decide to use these data items for any your publication, you agree to
refer to the original paper, where they are first used:
Machač, M.; Papuga, J.; Doubrava, K.; Fišer, J.: Fatigue Analysis of Thin-Walled Welded Hollow Section Joints. In: Fatigue and Fracture of Materials and Structures. Structural Integrity, Vol. 24, Cham, Springer 2022, pp. 49-55.
Weldments
Setup of the Experimental Campaign
- Tests performed at: Dept. of Mechanics, Biomechanics and Mechatronics, Faculty of Mechanical Engineering, Czech Technical University in Prague
- Test operators: Ivona Vízková (H-specimens), Martin Machač and Karel Doubrava (I-specimens)
- Testing machine: Amsler HFP422
- Load ratio: R=0.1
- Test frequencies: I-specimen 130 Hz, H-specimen 75-90 Hz
- Failure definition: Frequency decrease by 5 Hz
Experimental Results
H-specimen, R=0.1, f=75-90 Hz |
Sample | Stress amplitude [MPa] | Mean stress [MPa] | Number of cycles [-] | Defectoscopy |
H13 | 83.4 | 101.9 | 25799 | 1D: Incomplete penetrations 7.5 + 1.5 mm 2C: Pore 1.0 x 0.3 mm |
H07 | 83.6 | 102.2 | 29613 | 1D: Pore 1.0 mm |
H01 | 78.5 | 95.9 | 37890 | Between 2D and 2B: Row of pores 1.2 x 1.5 mm close to 2A: Pore 2 x 0.4 mm |
H11 | 67.9 | 83.0 | 41522 | 1D: Pore 2.1 mm close to 1B: row of pores 2.5 x 0.2 mm 1A: Tungsten 0.7 x 0.5 mm |
H09 | 73.3 | 89.6 | 69752 | 1D: Pore 1.0 mm 1C: Pore 0.4 mm 2C: Pore 2.6 mm |
H06 | 62.8 | 76.7 | 103827 | 2C: Pore 0.8 mm |
H14 | 57.6 | 70.4 | 166913 | 1C: Incomplete penetrations 1.5 + 1.5 mm 2C: Pore 1.3 x 0.6 mm |
H04 | 41.9 | 51.2 | 169279 | 1D: Incomplete penetration 8 mm close to 2C: Pore 1.2 mm |
H10 | 41.9 | 51.2 | 491391 | |
H08 | 52.4 | 64.0 | 497085 | 1D: Pore 0.5 mm 1C: Incomplete penetration 5mm 2D: Incomplete penetration 2.5 mm |
H05 | 36.7 | 44.8 | 1027905 | 1D: Incomplete penetration 4 mm 2C: Pore 0.8 mm |
H02 | 47.2 | 57.7 | 1124261 | |
H03 | 36.7 | 44.8 | 11231398 | close to 1C: Pore 1.1 mm close to 2C: Pore 1.0 mm |
H12 | 31.4 | 38.4 | 16734416 | |
I-specimen, R=0.1, f=130 Hz |
Sample | Stress amplitude [MPa] | Mean stress [MPa] | Number of cycles [-] | Defectoscopy |
T04 | 284.0 | 347.0 | 5817 | |
T11 | 260.7 | 318.6 | 7403 | |
T08 | 240.1 | 293.4 | 11105 | |
T06 | 195.9 | 239.4 | 20779 | Pore 0.7 mm |
T07 | 218.5 | 267.0 | 22961 | |
T05 | 173.3 | 211.8 | 31770 | Pore 2.2 x 0.5 mm |
T10 | 173.5 | 212.0 | 129927 | |
T02 | 120.7 | 147.5 | 198555 | Tungsten particle 0.7mm |
T12 | 150.9 | 184.4 | 270663 | |
T09 | 135.8 | 165.9 | 431158 | |
T03 | 120.7 | 147.5 | 836446 | |
T01 | 113.2 | 138.3 | 1264937 | |
papuga@pragtic.com | 















|